A current engine and management panel improve by CHP assist specialist Gen-C to Avocet Renewables’ 500 kW biogas plant at Coston Corridor Farm in Norfolk has delivered a 20% enhance in energy era and enabled 24/7 distant monitoring and administration of the system.
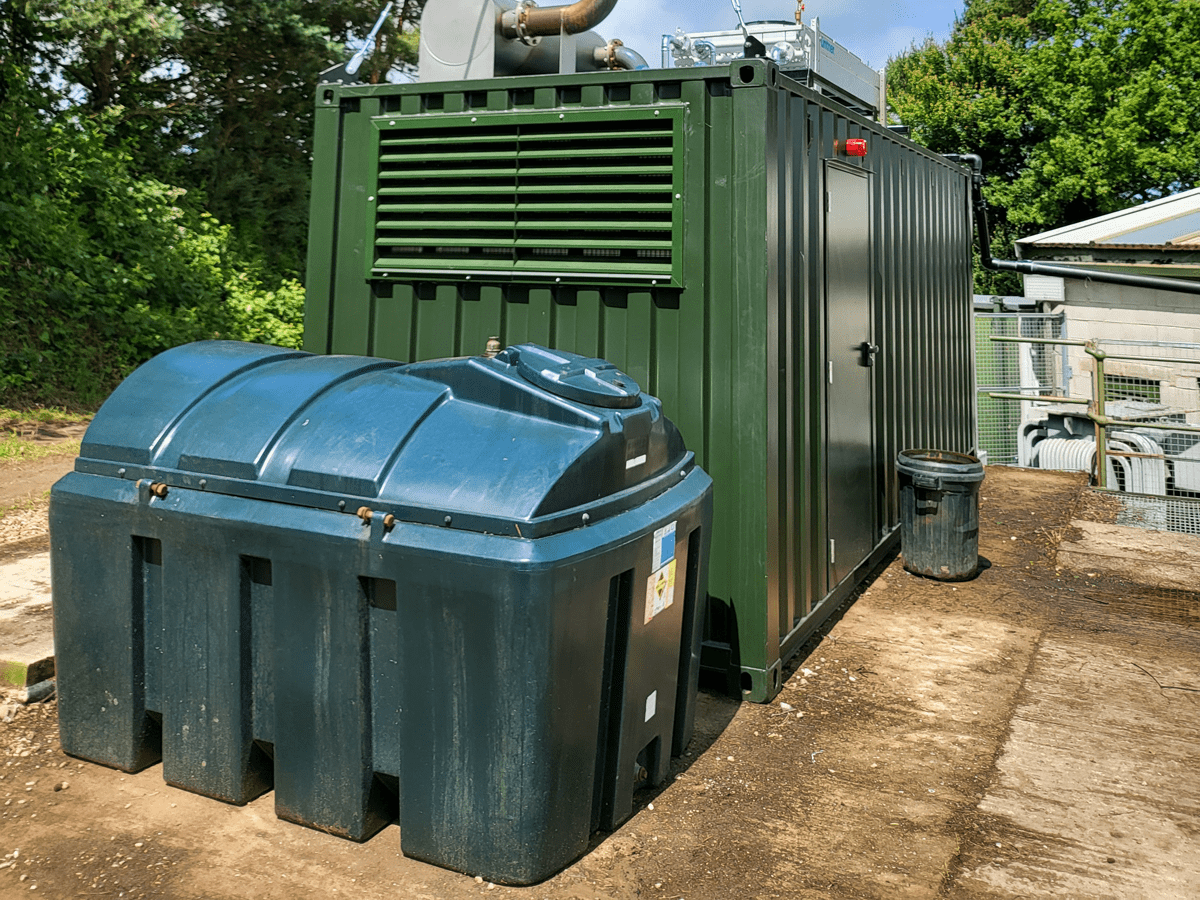
This publish consists of sponsored content material produced in collaboration with Gen-C.
The Avocet Renewables’ anaerobic digestion (AD) plant at Coston Corridor Farm, Barnham Broom close to Norwich makes use of agricultural feedstocks similar to power crops to generate biomethane and electrical energy, which is exported to the grid, in addition to warmth, which is used domestically on the farm for crop drying. The five hundred kW V12 MAN E3262 engine was put in in 2017 to supply warmth and generate electrical energy. Following a technical subject, Peterborough-based GenV Ltd have been introduced in to service and assist the engine. Nonetheless, points similar to a locked management panel meant that GenV have been restricted of their capacity to optimise CHP efficiency, so turned to assist companions Gen-C for assist.
Restricted by legacy controls
“The control system was old, and because it was locked to the original supplier we had no access to change key aspects of how the engine ran, and we couldn’t access anything remotely,” explains Warren Vessey, Managing Director at GenV. “After struggling for 18 months with failing engine performance, we performed a full R3 service and agreed with the client to undertake a number of upgrades, including a new open-access control system, with the help of our long-term partner, Gen-C.”
In addition to changing and upgrading the management panel, Yorkshire-based Gen-C have been additionally commissioned to improve the engine in a bid to revive misplaced energy output and enhance reliability.
“The engine was underperforming – producing only around 400 kW – misfiring and vibrating badly, so the client was losing considerable revenue” says James Thompson, Managing Director of Gen-C. “The engine was also comprised of a mixture of equipment from varying brands, which is something we see quite often – the ignition controller, actuator, fuel mixer, pick-ups etc. were from different manufacturers, which was impacting performance.”
Streamlining CHP operation
James continues: “To enhance general efficiency, we upgraded the important thing elements such because the mixer and throttle pace management. And since the whole lot we set up comes from one producer (main German model Motortech), the consumer now has a single level of contact for all servicing and spares – as we’re the only real Motortech agent for the UK. We concurrently eliminated the outdated controllers and display screen within the management panel and put in a brand new contact display screen with our controllers and growth playing cards.
“The new open-access control system means the AD operator, GenV and ourselves can all access the system remotely and make immediate changes as required, keeping downtime to a minimum. The system also features smart diagnostics, with alerts based on user-defined parameters, and is backed by our 12-months free remote technical support.”
Advantages of distant entry
Probably the most speedy profit loved by Avocet Renewables following the engine improve is that their CHP is as soon as once more operating at full energy, offering a 20% uplift in output. With the brand new elements designed to final for not less than the following ten years, the engine can also be working extra easily which is able to enhance reliability, reduce downtime and scale back servicing necessities.
“The open protocol on the new control panel gives us full access to the engine via remote monitoring. That means I can see everything that’s happening and can assist the Coston Hall Farm site at any time, from wherever I am, making it far more efficient and easier to use,” stresses Warren Vessey.
“Another big advantage for the client is that they now have full flexibility and choice over who handles their maintenance contract. It’s an industry-known system with readily available parts and support, so anyone can access it. It’s user friendly and modifications or adjustments can be made from anywhere, which really helps to limit downtime.”
The improve was solely accomplished in mid-June, however Mark Gill, Plant Supervisor at Coston Corridor Farm, is already constructive: “The system works well and is a lot speedier than the old control panel. It’s also much easier to operate and, most importantly, our CHP is operating at full power again.”